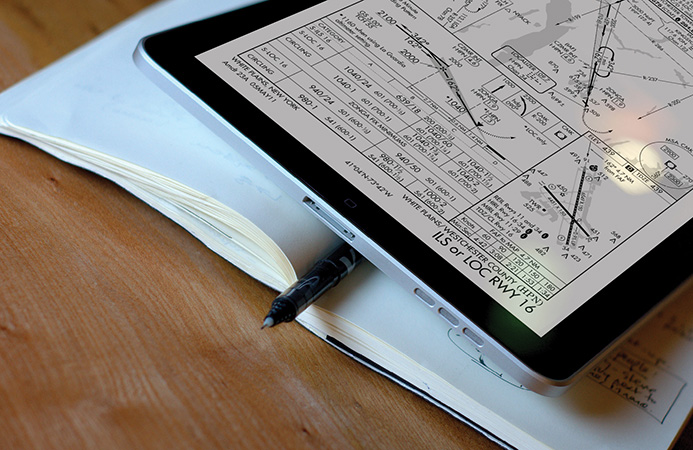
Download article in PDF format
World Aircraft Sales, June 2013
by Ken Elliott
Electronic Flight Bags (EFBs) represent one of those revolutionary technologies that transform cockpit management. It’s a technology with multiple applications for potentially minimal cost, streamlining aircraft operations while reducing both aircraft weight and environmental impact.
One major US Airline estimates that it will save 326,000 gallons of jet fuel a year and 16 million sheets of paper by replacing traditional paper-based flight bags with iPads across its fleet.
Unfortunately, as with many emerging and rapidly evolving aircraft technologies, authorization for use is a certification puzzle.
The operator is not simply approving an installation but also flight bag operations for that specific flight department. New aircraft owners may be spared that effort as production aircraft are delivered with single or dual flight bags standard, or as an option – in which case the aircraft OEM has typically covered the bases and ensured the installation and operation can only be within regulatory requirements.
In the US, an Airworthiness Circular AC120-76B issued in 2012 acts as the primary guidance for installation and operations of EFBs. In Canada it is AC700-020, while EASA uses TGL-36 and ICAO – representing many international regions – has an EFB sub-group that will finalize recommendations regarding the use of EFBs sometime in 2013. Many other proactive regulatory agencies such as Australia, China (including HK SAR), UK and Sweden have advanced guidance based on US and EU advisories.
Given that most of the guidance material is similar across the world, we will focus on US guidance. This should be a good starting point for anyone trying to grasp a basic understanding of EFBs, their installation, and their use in the cockpit. Some cockpit-based systems have a higher need for understanding human factor implications. Anyone considering upgrading to EFBs should pay careful attention to cockpit resource management. Note also that most cockpits will employ dual EFBs.
As for classification, EFBs are categorized by their hardware and software. The hardware class focuses on the extent to which the device integrates into the cockpit, while the software type focuses on how the use of the EFB relates to the performance and operation of the aircraft.
EFB HARDWARE CLASSES
Class 1 EFBs: These are Portable Electronic Devices (PED), stowed below 10,000ft, that are not normally used during take-off and landing operations, and do not require an administrative process to remove them from the aircraft. Connectivity to other aircraft systems should be read-only.
They can have quick disconnect aircraft power and limited read-only interconnect. Because they must be stowed for take-off and landing they have limitations as to when they can be used.
Class 2 EFBs: These are Portable Electronic Devices (PED), normally mounted in a position where they are utilized during all phases of flight and require an administrative process to remove or replace them from the aircraft. Fixed equipment used to mount or interface to an aircraft requires design approval. There can be limited connectivity to other aircraft systems and data such as weather. Aircraft mounts include power and interconnect, but for egress the device should still have a quick disconnect capability.
The device can be used to compute weight and balance information as well as take-off and landing speeds, and to display flight critical pre-composed data, such as navigation charts. Since it is not necessarily stowed for take-off and landing, pilots can use it to display departure, arrival and approach charts. Class 2 EFBs typically include a separate aircraft interface module.
Class 3 EFBs: These are fixed, installed equipment and therefore require installation design approval, typically implying that an STC will be necessary. Depending on the model, it may be connected to the GPS or FMS and it may be able to combine GPS position with the locations and speed vectors of other aircraft as well as provide graphic weather information into a single, detailed moving map display. Its detailed database can also provide obstacle and terrain warnings.
EFB SOFTWARE TYPES:
Type A Applications
• The least complex software providing electronic documentation such as flight manuals but no navigational charts.
• Requires operational approval.
• Examples include: Non-interactive manuals, logs, data sheets, records and operational guidance material.
Type B Applications
• Provides all Type A information: can display approach charts, calculate weight and balance, and deliver weather information.
• Requires operational approval.
• Requires regulatory agency evaluation.
• Examples include: Aeronautical charts and maps, interactive performance calculations (such as takeoff, en route, and landing), weight and balance calculations, weather and aeronautical data, etc.
Type C Application
• Provides all Type A and B information and can display “own-ship” position on approach and airport charts. Uses approved aircraft standard avionics data known as DO178B compliant. Type C applications can include weight and balance and other performance related data for specific aircraft models.
• Requires operational approval.
• Requires regulatory agency evaluation.
In summary the more an EFB physically and electronically integrates to an aircraft and its performance, the more certification effort is required to install and operate it. Note also that the regulatory authority will look at the category of aircraft operation when approving EFB use.
A commercial airline or charter/fractional operator will incur closer scrutiny, particularly to the EFB operation or its intended use. The goal of the authorization is to ensure risks are mitigated and safety assessments completed.
An aircraft crew should be able to operate the EFB in a seamless fashion, dovetailing it into the existing cockpit procedures. In fact it is recommended that a transition period from paper to paperless should include an overlap of several months when both paper and paperless are available to the crew at all times.
ADDITIONAL CERTIFICATION GUIDANCE
Apart from the primary guidance material already mentioned, some of the more useful additional Airworthiness Circular (AC) guidance material and breakout of class and type certification is provided below:
• AC 91-78 use of Class 1 or Class 2 EFBs.
• AC20-159 airport moving map display ‘own ship position’ Class 1 and 2 EFBs for use on the ground only.
• AC20-173 installation of EFBs.
• AC91-21-1 use of portable electronic devices (PEDs).
• AC20-64 electronic checklists.
Class 1 EFB: Certification requires an assessment of the physical use of the device in the cockpit, possible risks associated with electromagnetic interference and the use of lithium batteries.
The EFB power source must be capable of deactivation at any time. It may even be appropriate to have an alternate power supply available. The EFB may not be connected to any aircraft system but may be connected to non-aircraft systems on the ground only.
Class 2 EFB: Certification requires a regulatory approval of the mounting arrangement, its ability to withstand impact when mounted, its data connectivity and its power connection. Also required is an assessment of the physical use of the device in the cockpit, possible risks associated with electromagnetic interference and the use of lithium batteries.
The EFB power source must be capable of deactivation at any time. Data connectivity and isolation from other aircraft systems should be validated while ensuring non-interference. Typically data connectivity to aircraft systems involves an STC process.
Class 3 EFB: Certification requires a full airworthiness approval (STC) just like any other on-board avionics system. A Class 3 EFB may form part of a network supporting other functions. A human factors and safety assessment will be part of its evaluation.
Type A: Can be used for document storage and retrieval.
Type B: Can be used for independent performance calculations, the display of charts with no aircraft position and checklists, can use the internet, and display weather and external cameras (one example being heads-down enhanced vision infrared imagery).
Type C: Relates to the active control of the aircraft in flight raising significant human factors concerns. This usually requires the EFB system to be Class 3.
Part 91 operators in the US and as pilot-in-command, may approve the operation of their own Class 1 and 2 EFBs, but Part 91K, 135 and 121 operators must obtain operational approval though the OpSpec process. Under
EASA and other regulatory regions an OpSpec or alternative form of operational approval will be necessary for all users. For those readers who are members of NBAA, you will find a wealth of useful EFB operational data under the Association’s aircraft operations portal.
EFB BRANDS BY CLASS
There are a plethora of EFB devices available today and in a sense they follow the three hardware classifications discussed. Commercial off the shelf (COTS) devices include the beloved iPad and popular Android devices. COTS devices are found in both Class 1 and 2 applications.
Aviation equipment manufacturers, meanwhile, have taken the COTS principle and adapted specific units for aircraft mounting and digital interface. These devices are designed for aircraft and include physical characteristics suitable for aircraft reliability and performance. Several industry leaders have emerged in Class 2 and 3 arenas such as Universal Avionics (the first to market with Class 3 certified), CMC, navAero, Astronautics and Goodrich. And there are an even greater number of application providers supplying a wide array of software for use on all classes of EFBs.
WHY EFBs
Some key benefits for using EFBs in the cockpit are:
• Reduced pilot workload
• Efficiency
• Safety
• Replacement of paper reference
• Reduced cost
• Weight saving.
An example of features that can be gained from a full Class 3 EFB system shows just how beneficial Electronic Flight Bags can be in terms of what they provide:
• Airport Map/Runway Incursion Prevention
• ADS-B Merging and Spacing
• Enroute Moving Map with dynamic own ship position
• Aviation Weather Information
• Network Connection
• CPDLC
• Communication Management Unit
• Data Loading
• Maintenance
• Charts
• Manuals
• Video Surveillance
• Request Application Information
• Others.
TRAINING
Finally the importance of training cannot be reinforced enough. Incorporating new cockpit tools into the normal flying procedures can be complex and time consuming. Some operators have used their COTS and PEDs to interface with existing X-Plane commercially available software creating realistic simulation of the cockpit environment. This allows for the new devices to be proven and tested down to simple processes like folder management for the many documents available on the device.
This ground based proving exercise can be a very effective way of establishing a flight department-standardized procedure for using EFBs in flight operations.
❯ Ken Elliott is an avionics veteran of 40 years and more recently focused on NextGen. His work within the NextGen Advisory Council sub-committees brings him close to current and intended development effort. Equally, his specialization in low-vision operations provides a deeper insight into one of the pillars of NextGen. Ken has served the aviation industry on three continents from light GA to large corporate aircraft. His current employer Jetcraft is a leading aircraft brokerage company with worldwide presence. More from www.www.jetcraft.com, email: [email protected]
SIGN UP FOR OUR MONTHLY JETSTREAM RECAP
Don't miss future Jetstream articles. Sign up for our Jetcraft News mailing list to receive a monthly eblast with links to our latest articles. Click to join the 1,800+ subscribers on our mailing list.