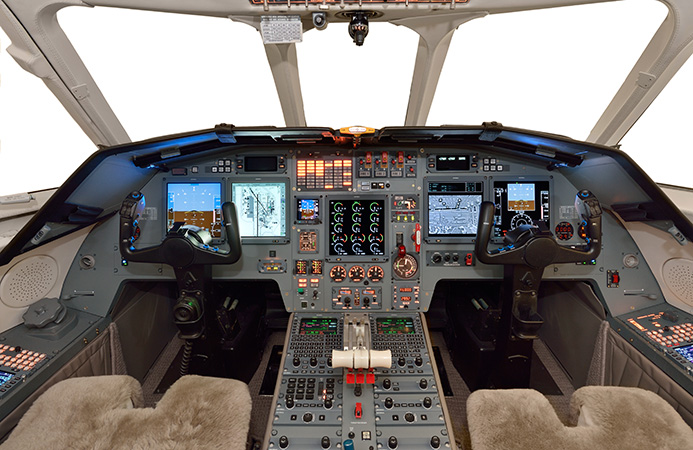
AvBuyer Magazine, June 2015
by Ken Elliott
Download a PDF of the article.
Helping you understand avionics advances and related requirements for equipage, Ken Elliot reviews aviation technologies within the NextGen/SESAR architecture, this month focusing on the installation aspects of avionics mandates.
With only 6.5% of the total US-based aircraft equipped for ADS-B, there is a significant need for installation capacity between now and January 2020, the deadline for ADS-B Out equipage. Clearly, the Maintenance, Repair and Overhaul (MRO) community will be hard pressed to fulfill the demand.
As a rough guide focusing on turbine business aircraft, Table A shows that each US MRO needs to complete an average of 4.7 aircraft per month between now and 2020 for everyone to meet that country’s deadline. (Note that MROs owning multiple locations have greater capacity to achieve the monthly quota.)
General Installation
When shopping for a location to handle your aircraft’s avionics upgrade, keep in mind there are two primary paths to follow:
• Original Equipment Manufacturer (OEM) core facilities including OEMowned facilities worldwide.
• Maintenance, Repair and Overhaul (MRO) facilities including OEM-authorized service centers.
When it comes to equipage, pathways can become complex. For an OEM, the solution may be developed via a Type Certificate (TC) or a Supplemental Type Certificate (STC). For an MRO, the solution is developed via an STC.
Factory approved solutions provided via OEM: This path is where the standard aircraft ‘new-build’ avionics suites are upgraded or added to in order to meet requirements. Although developed via a TC or STC, the aircraft OEM issues the change as a service bulletin or factory modification to operators.
Very often the aircraft must return to an OEM facility for the work. Be careful as modifications may occur in phases and be aircraft model- or serial number- specific.
MRO in partnership with Equipment Providers: This path is specifically used when the equipment provider wants to own or have usage rights to the STC. A partnership is created with an MRO to develop the STC on a candidate aircraft.
While the MRO may have the advantage of owning the STC, the facility typically cannot be exclusive users of its data. This means other MROs can implement the STC but the equipment provider controls the data. On occasion, the equipment provider will agree to an exclusivity clause, typically allowing for 12 months of singular market share capture.
MRO STCs supported by Equipment Provider: Even though the MRO independently develops the STC, the facility is supported by the equipment provider. Equipment providers support this path when they do not see enough of a business case to go into partnership for an STC. MROs developing these STCs may elect to hold data exclusively for their own use. In this instance an operator must select that specific MRO for the upgrade.
Several years ago it was common for MROs to make their STCs exclusive, thereby creating bad blood. Today, in the best interest of the avionics industry, most MROs are moving away from that trend.
MRO STCs using avionics that differ from original equipage: This path is very common for older legacy aircraft where neither the equipment provider nor the aircraft OEM has a desire to provide a solution, with cost often the decider. Similar economic factors drive these STCs to use mixed equipage; so called ‘happy boxes’ providing interface between old analogue and new digital technology are commonly deployed.
Do not expect an easy ride with these STCs as both cost and risk typically climb; but occasionally innovative, low-cost STCs are developed by more entrepreneurial avionic facilities. It is important to note that, as a general rule, installation difficulties increase exponentially as mandate deadline dates draw near.
It makes a lot of sense to bundle together upgrades like FANS and ADS-B Out as well as timing them to coincide with major inspections, interior rework or paint. However, combining paint and avionics may not help, as your aircraft will be buried in the paint hangar for much of the time.
When trading an aircraft, read its specifications carefully. “Provisioned” means just that, and often the bigger chunk of the work awaits you. Especially for Data Com, there are several phases and there are misunderstandings interpreting CPDLC, FANS and ADS-C.
Earlier articles in this series explain these Data Com areas, but it is recommended you sit down with an avionics specialist at your aircraft OEM or MRO to map out the requirements needed, and how best to accomplish them. You will be glad you did!
Access
On the aircraft side, primary NextGen technologies are: Data Com (Mandated); ADS-B Out (Mandated); PBN/RNP/WAAS-LPV (Required, based on operational need); and TCAS 7.1 or later (Mandated). Each has unique installation access considerations, but downtime is of particular interest to operators.
When avionic facilities quote installation downtime, be careful to ask if the cost and time for interior repair and refurbishment or access is included. Because these facilities often leave access as an additional cost due to its variability, more downtime is implied. Access is a major consideration for work scope bundling. Opening the aircraft’s interior only one time for a broadened work scope involves less risk and less wear.
Opening up the cabin and specifically removing headliners is a major access concern. If the headliner is ‘one-piece’, you can only imagine the access labor required.
Cabin and headliner access is primarily reserved for antennas and wire runs, including antenna cables. A specific antenna concern with NextGen technology is the replacement of GPS antennas. While Flight Management Systems on aircraft already have GPS antennas, it is possible they may need to be replaced to accommodate ADS-B Out and PBN position accuracy requirements. The aircraft headliner will need to be removed if GPS antennas are mounted atop the cabin and if their footprint changes. A concern like this should be addressed early with the avionics facility.
Another concern centers on antennas required for Satcom ADS-C and if the desire exists to add intercontinental WiFi. While many Satcom, Inmarsat or ViaSat antennas are mounted atop the aircraft tail, Iridium (domestic) antennas are usually mounted atop the fuselage. When selecting Satcom options, you should also discuss antenna type and location with the avionics facility.
Lastly, with respect to access, it is assumed the aircraft already has a full TCAS II system onboard. For the TCAS 7.1 upgrade, the only need for access should be to reach the processor and maybe to add minor wiring for ADS-B Out.
Note: For any NextGen technology already certified on your model and serial number aircraft, downtime should not be dependent on the length of the certification process.
Specific Programs
A great starting point for ADS-B Out programs is the FAA NextGen website. Because of GA pressure there has been significant effort expended to provide meaningful data to the aviation community. After spending a few minutes on the ‘Equip ADS-B’ portion of the FAA site, users will quickly notice the helpful results. This region of the FAA website includes a current updated list of ADS-B Out STCs (www.faa.gov/nextgen/equipadsb/equipment/).
For FANS/CPDLC, the program status is different. For aircraft covered by an aircraft OEM program, the path is easier to navigate, starting with a call to the aircraft OEM’s avionic specialist. Bear in mind that some reputable MROs are authorized to complete aircraft OEM service bulletins and if one of those MROs is your normal service location, there exists options for the MRO to undertake factory-authorized upgrades.
Creatively, MROs are now working with Satcom equipment providers such as Gogo-Biz, ICG and True North as well as major avionics suppliers Rockwell, Honeywell, Universal and Garmin to provide economical FANS (and ADS-B) solutions. These solutions offer other NextGen benefits because the updated GPS provides greater accuracy. Precision PBN, better Satcom data services and display dependent ADS-B In are some indirect benefits.
MRO STC programs are now emerging and are often in competition with each other. See Side Bar A at the end of this article to view a listing of some of these.
Cost
While not delving into actual numbers, there are general costs to consider. Access is one area where unexpected fees can creep in, as mentioned above. Each aircraft is unique, especially as it ages and it’s interior layout changes. It is common for access costs to be a major portion of the work scope on aging aircraft. Another area for cost creep is additional work scope based on ‘aircraft not seen’ or subject to a ‘review of avionic diagrams’.
Following are ‘catch all’ buckets where costs may occur unexpectedly, most with justification by the avionics facilities.
• Provisions including hardware and wiring, listed but not actually in the aircraft.
• Equipment still listed but in fact changed since aircraft delivery.
• Equipment part numbers not as listed.
• Equipment software levels not as expected.
• Position of equipment not in its factory standard location.
The way to avoid additional costs is to keep good records, share all your data with the avionics specialist and create your own ‘to do’ list of questions, covering these and other concerns. Reputable equipment and maintenance tracking programs are also available. They are helpful in preventing installed equipment and part number errors. Most major installations require a flight test or two that involve fixed and variable operating costs not borne by the installation facility.
The hassle of extra downtime and the stress of things going wrong are best avoided, so be prepared and educate yourself on the NextGen technology. Network with the wider aviation community, and always ask questions up front.
Location
The location you select for your aircraft is critical in so many ways. There are many factors to consider, and no one selection process fits all. The important elements of trust and relationship by far top the list. After those, consider the following:
• Hangarage, and specifically where your aircraft will sit for the major portion of its downtime.
• How will your aircraft be protected during its stay?
• Who will be working on your aircraft and especially, who is taking it apart?
• Who is the crew chief, engineer and the certification specialist? Get to know them!
• Facility capability, including airframe and engine?
• Educated questions asked beforehand, the level of detail in the Proposal and the professionalism of any communications before you agree to sign.
• Proposal pricing, but perhaps more importantly Terms & Conditions.
• Training and product support, including for the installation itself.
• Will assistance be provided for operational approval?
• Facility location and logistics that impact you. Having a customer office is very helpful!
Timing
Looking at Table B, it could be said that timing is everything, but the timing impacts of operator planning, budget and schedule are equally important. It is not always possible to plan well ahead, and even best made plans may need to be changed. For an operator, predicting the short-, medium- and long-term plan for the aircraft will help determine slot times for service. Combining major maintenance with an upgrade is the best way to go with major inspection dates predicated on projected flying hours.
If trading an aircraft, the operator has the difficult decision to make of whether to upgrade and add to the sell price, or sell as is. There are good arguments for both approaches, but one way to view the question is: If your aircraft, fully-equipped and compliant for all avionic mandates, is sitting on the ramp next to an equivalent aircraft that is not fully equipped and priced correspondingly less, which aircraft will sell first?
Because the equipped aircraft is a known quantity and the unequipped has all the required implementations still to go (and is therefore an unknown quantity), it could be assumed that the equipped aircraft will sell first. It has the edge and none of the risks or concerns covered within this article to face down the road.
Training & Operational Approval
In today’s environment, equipment plus installation and certification are well understood and implemented. However for a slew of reasons, training and operational approval are neglected areas, with resources unapplied and experience lacking. The NBAA has recently taken on this concern specific to cabin connectivity issues, where it has been shown that lack of training is a key contributor to common aircraft connection problems.
If the avionics facility does not offer training or assistance in obtaining international (or domestic) operational approval, the quality of service you will receive during an upgrade may be deficient.
Operational approval should be planned well ahead. Hold an initial meeting with the aviation authority prior to starting work on the aircraft. Ensure operational approval is achievable before any funds are spent or work commences on the aircraft.
Each aviation authority has its own approval process, and their websites provide the avenues to follow. Knowing projected domestic and world operation regions for your flight department will allow proactive planning of approvals to be authorized once the aircraft installation is complete.
Are you looking for more articles on avionics? Visit www.avbuyer.com/articles/category/business-aviation-avionics/
❯ Ken Elliott is a highly-respected industry authority on avionics as a member of the NextGen Advisory Council sub-committee and Technical Director, Avionics at Jetcraft. Contact Ken via [email protected] or www.www.jetcraft.com.
This article was written by Ken Elliott, Jetcraft Avionics – Technical Director, for AvBuyer Magazine. It was published in the June 2015 issue. Click here to view the Digital issue of the June AvBuyer or to view Archived editions.
Header Photo courtesy of Duncan Aviation, Inc.. Duncan Aviation recently completed its second installation of Universal Avionics’ EFI-890R cockpit upgrade in Falcon 900Bs. This upgrade replaces 25 older instruments and significantly improves reliability and situational awareness.
MRO STCs
MRO STC programs are now emerging and are often in competition with each other. Following are some of them…
Clay Lacy: Gulfstream GIV, GIVSP & GV FANS STC including CPDLC, ADS-C and provisions for LINK 2000+ and ADS-B Out. Clay Lacy’s website covers the program (including a useful White Paper).
Comlux: Challenger 600 series. FANS STC involving a partnership of equipment manufacturers (e.g., Universal Avionics, ICG and L3). This solution offers CPDLC, FANS over Iridium (FOI) and the required Data Com recording capability.
Duncan Aviation: Dassault Falcon 900B and Falcon 2000 using a Universal Avionics solution for CPDLC, FANS and ADS-B Out.
Chicago Jet: Dassault Falcon 50, 900 and soon 2000. Also advancing on solutions for the Gulfstream GIV, GIVSP, GV & G100. Several other aircraft types are also in work.
Other programs are offered by Jet Aviation and Standard Aero. Many worldwide facilities, including those offering major aircraft refurbishments, bundle mandated avionics upgrades either as available from the aircraft OEM or under license from an STC holder. Also versatile international avionic companies such as Scandinavian Avionics and Hawker Pacific (Avionics), well represented in many areas of the world, are capable of meeting operator NextGen equipage needs.
SEE AVBUYER, JANUARY 2015 FOR A FULL LIST OF BUSINESS JET CAPABLE OEMs AND MROs.
SIGN UP FOR OUR MONTHLY JETSTREAM RECAP
Don't miss future Jetstream articles. Sign up for our Jetcraft News mailing list to receive a monthly eblast with links to our latest articles. Click to join the 1,800+ subscribers on our mailing list.